Internal Turbine Needle Valve Inspection
For this project, the customer suspected that incorrect operation of the needle valve and deflector plates in their Pelton turbine were causing a scenario where upon shut down, the turbine had the potential to reverse direction. This was a theory, but they wanted to commission an inspection to determine if that truly was the case so that they could take corrective action. The customer had previously worked with Hibbard Inshore on a number of penstock inspections and called them due to their extensive experience with underwater inspections. Hibbard Inshore devised a solution to allow video of the turbine to be taken during startup and shutdown. They were able to mount the same underwater cameras used on their ROVs to be placed inside the turbine during start up. The cameras were mounted in such a way as to be able to visually confirm the behavior of the needle valve and deflector plates, and upon turbine shutdown it was seen that indeed the deflector plates were deflecting some of the water in the opposite direction as intended. This allowed the customer to properly retrofit the system so that the turbine would not continue to reverse in fast shutdown scenarios.
Sensor Array Retrieval
This job involved the retrieval of scientific research sensor array systems with anchors at over 1300 feet of depth. The project is one that Hibbard Inshore has been repeatedly hired to complete as the retrieval of each array involves hazards due to the cabling systems and the location of the arrays. The client had past difficulties with other ROV operators who had become tangled while trying to complete the project. Upon consideration of the project, Hibbard Inshore realized that a swimming ROV with sufficient power to negotiate the currents involved at that depth coupled with sonar, navigation, and tracking systems would be necessary to safely avoid tangle hazards while keeping costs down and not requiring the use of a costly dynamic positioning vessel.
Array Retrieval Barge and Work Vessels
Hibbard Inshore selected a vehicle from their fleet, their Sub-Atlantic Mohican, that could hold the appropriate sensors and manipulator, achieve the depth, avoid tangle hazards without the use of a DP vessel, and was still small enough that the ROV could be shipped by air to the project’s remote location at a moment’s notice each time the customer determines they need assistance in reconfigure the arrays. The vehicle was fit with dual imaging sonar units, a 4 function manipulator, a ultra-short baseline tracking system, and a navigation suite connected to GPS on the vessel of opportunity used for operations. The vehicle was used to retrieve the ROVs belonging to the other contractor and then to perform the array retrievals. Hibbard Inshore has been able to successfully complete this retrieval process several times where previous attempts had not been successful.
Crawler Inspection of Long Produced Water Lines
This project involved Hibbard Inshore performing the inspected a series of produced water lines in the Oil and Gas industry. These lines, ranging in diameter from 12” to 18”, were of significant concern to the customer because they could not be pigged using traditional smart pig technology. This was due to a number of the lines having significant bends and changes in diameters of the pipe. There were also concerns for the pipes’ integrity if they were to be put under significant pressure as would potentially occur during pigging. A number of the lines run under stretches of open water, and the crawler allowed the customer to avoid undue stress on those sections.
Crawler Entering Line
With smart pigging not being an option, Hibbard Inshore used an Inuktun crawler vehicle (Link) to inspect the pipelines. Using individually articulated tracks for propulsion and an adjustable chassis, the Inuktun crawlers can crawl out to a range of 5,000 linear feet, and can navigate around bends in even relatively small diameter pipelines. For this inspection, the crawling ROV carried a tilt and rotatable color video camera along with both adjustable spot lighting and flood lighting, stopping to inspect any areas of interest. Prior to the inspection, the lines were purged by the customer to eliminate explosion hazards.
Inspected Pipeline with Elbow
The long distance crawler gave Hibbard Inshore the ability to inspect the entire length of each pipeline, recording video footage of all notable features which were reported to the client along with their locations. The crawler’s versatility along with strength and gripping ability of its tracks allowed it to move through significant bends while maintaining traction even at great distance. The result of the inspection was that the crawler was able to identify areas of interest including light spalling, split gaskets, and hairline cracking in both the longitudinal and circumferential directions allowing the customer to plan maintenance activities accordingly.
Recovery of a Pipe Coupon Located 4,000’ from the Access Point
Surge Shaft for Mohican Access
This project involved a hydroelectric intake tunnel where the customer had hot tapped the pressure piping in order to divert a portion of the water for another purpose. During the hot tapping by the contractor, there was a malfunction, and the pipe coupon could not be extracted by the hot tap equipment. The coupon fell into the pressure pipe. Since the coupon was of significant size, it posed a hazard to the hydroelectric facility and its turbines. The decision was made that it would have to be removed from inside the pipe. Since the location of the hot tap was approximately 4,000’ from the location of the nearest access point into the tunnel at the surge shaft, Hibbard Inshore was called to provide an ROV and extraction tooling that could not only fly the distance to the coupon and locate it but also remove it through the pressure piping and shafts while the tunnel and piping remained flooded. Hibbard Inshore was up to the task, quickly devised a method, designed ROV tooling, and mobilized to site to assure the coupon would be removed.
Mohican ROV with 4 Function Manipulator
Due to the need for a Remotely Operated Vehicle (ROV) with the ability to retrieve the coupon, a larger light work ROV was used instead of a standard inspection ROV. It was decided that Hibbard Inshore’s Sub-Atlantic Mohican ROV with 4 function hydraulic arm would be the proper vehicle to retrieve the coupon.
Upon arrival at site, it was assumed that the coupon was either in the immediate area of the hot tap or slightly downstream at the lower elbow of the vertical tunnel section. While traveling in the horizontal section, the ROV’s forward looking sector scan sonar was used to image the invert of the tunnel and look for the coupon. When the coupon was located, the ROV manipulator picked up the coupon with a special hook. The hook was built specifically for the retrieval of the coupon by inserting the hook through the hole in the center of the coupon.
Mohican and Coupon Lowered to Ground
The ROV searched for the coupon as it entered the tunnel but focused on the lower elbow below the vertical section. Then, the ROV travelled up the vertical section and located the hot tap on sonar. The ROV moved to the hot tap location and quickly found the coupon in the invert of the pipe, immediately below the hot tap. A detailed visual inspection was performed of the hot tap to tunnel interface which was on the left spring line of the tunnel when facing up stream. Once the inspection was complete in the hot tap area, the manipulator engaged the coupon. Once engaged, the ROV travelled with the coupon downstream to the lower elbow of the surge shaft.
Recovered Steel Coupon
After the coupon was recovered, a tunnel inspection was performed from the surge shaft upstream (approximately 3,800’) to the lower elbow of the vertical section. The area above the vertical section was inspected during the coupon retrieval stage. Both the coupon retrieval and the tunnel inspection were performed with very low water clarity. The ROV Used two sonar heads, one recorded the cross section of the tunnel while the other scanned for features forward of the ROV during the inspection phase.
Hole Plugging in an Active Surge Shaft
In 2010 Hibbard Inshore was contracted to provide an inspection of the surge shaft at the Tala Hydroelectric facility. During this inspection they were able to identify several holes with active flow in the bottom of the concrete surge shaft. This discovery was of concern to the owner as they were afraid that this may eventually affect the stability of the structure. Shortly after the inspection, the plant owner, the construction company responsible for the construction of the surge shaft, and Hibbard Inshore all proactively looked for solutions to permanently stop the flow through these holes to prevent further degradation. Since the plant provides a great source of power and revenue for the region, it was determined that solutions for plugging the holes that would allow the plant to maintain its normal generation schedule each day would be necessary. The generation schedule allowed for 8 hour shutdown periods each night. This meant that all equipment involved with the hole plugging would have to be inserted, operate, and be removed from the shaft during each 8 hour period so that the plant could operate each day.
Hole with Protruding Material from Initial Inspection
The access to the area where the holes were located was through the top of the surge shaft. The surge shaft at the Tala facility is located underground and is accessible through a tunnel. The surge shaft is approximately 180 meters in height with approximately 100 meters of water depth under normal operating conditions. Because the rate of flow through the bottom of the surge shaft is around 10 meters per second under normal operating conditions, it was determined by the owner that all materials involved with the hole plugging project would need to either be securely and permanently fastened in each hole or would need to completely be removed from the surge shaft each day prior to the scheduled generation. They required a solution that did not introduce unnecessary hazards that could flow into the penstocks and risk damage to the turbines.
Hibbard Inshore 5 km Sub-Atlantic Navajo and 2 km Seabotix LBV for Initial Inspection
A project of this exact nature, to the team’s knowledge, had not previously been performed without manned entry. In this case though, it was determined that the costs and risks of a manned entry to make permanent hole repairs without dewatering at 100 meters of water depth, with the restriction of 8 hour outage periods, confined location, and the high flow rates in between outages would be prohibitive. Due to the short outage times, the confined nature of the work, and the depths involved, it was determined that utilizing an ROV provided both safety and economic benefits over attempting to use a commercial dive team.
Hole with Particulate Flowing through Surge Shaft Floor
Upon conferring with the Hibbard Inshore team which included Dr. Ray Henn of The Colorado School of Mines and Brierley Associates, the first option that was discussed was to devise a method to pump grout from the surface into each hole while leaving the shaft flooded. In this scenario, the Hibbard Inshore ROV would be able prepare each hole for grouting by clearing it of debris using an onboard saw and a hydraulic drilling system. Once the hole was cleaned out, a customized grout packer would be inserted to allow the ROV to attach the grout hoses from the surface and the grout to be pumped into each hole.
It was determined that an approach including grout pumped from the surface would be very risky due to the fact that it was unknown how large of a void exists underneath the surge shaft slab. Because of this, it was unknown how much grout would be needed to sufficiently fill each hole. It was also unknown as to whether each of the holes communicated with the others under the shaft. Worries were that the grouting would need to be performed very quickly in a single 8 hour shift at each hole so that the grout could properly set and that pressure differentials would need to be closely monitored to avoid placing forces on the slab that would result in a potential disaster due to cracking or heaving.
It was decided that the engineering issues for grouting were going to be complex. Understandably, the owners were looking for a lower risk option that could be completed quickly to reduce or eliminate the flow through the holes. During this discussion time, through additional investigation, the owners identified the exit path of the water from inside the surge shaft and determined it exiting through the side of the mountain. This development caused concern that there could be undermining occurring and increased the importance of identifying a good method to plug the holes as soon as possible. Because of this accelerated timeline and the complexity of the grouting scenario, the grouting option was set aside in favor of providing customized plugs to fill each hole.
Packer CAD Model
Upon deciding to plug the holes with customized plugs, it was determined that the concrete placed to create the slab at the bottom of the surge shaft was M20 concrete. This was important because it allowed the Hibbard Inshore team to determine that specialized plugs based on grouting packers could be placed into each hole and inflated to complete a seal without damaging the concrete. It was not known whether the holes were lined with pipe or if the seal would need to be made directly with the concrete; so, the team tested to insure that the plugs would work in either scenario.
The packer plugs were specially designed to be inserted by the ROV, to have the water hoses for plug inflation hooked up and unhooked by the ROV, and then to be secured into place by the ROV filling them with epoxy. Each packer plug was made from stainless steel and was coated in vulcanized rubber to provide a sealing surface. The packer plugs were specially designed in order to create a seal while not exerting forces that would exceed the compressive or tensile strengths of the concrete. In addition, the design considered that the plugs should require great force to remove them from each hole as they were meant to be a long term solution, and they would be in place during the high flow conditions caused by normal generating operations. After discussion of other possibilities, it was determined by the owner and construction company that this was the best method for repair, and the Hibbard Inshore team was hired to design the packers with Baski Inc. of Denver, Colorado so that they could be inserted by the Hibbard Inshore Sub-Atlantic Mojave ROV.
Packer Final Construction
The packer plugs were designed, fabricated and tested in the Baski facility under the direction of Hibbard Inshore and Dr. Henn, and were shipped to Bhutan for installation in early April of 2012. Several sets of packers were manufactured in order to account for the possibility of varying sizes of holes. The hole sizes were estimated from the previous inspection, but it was not known how the holes might have changed since that time, and due to the urgency of the project, the owner, construction company and Hibbard Inshore all agreed that Hibbard Inshore should come prepared for a variety of scenarios.
Figure 9 Packer Cap with Floats for Retrival after Disconnect
Upon arrival at site, the Hibbard Inshore ROV was deployed to first measure the holes to determine if there had been any noticeable change from the previous inspection in 2011. The ROV was deployed to the bottom of the surge shaft, and measured each of the holes to confirm that they had not changed in size or nature since the previous inspection. Upon confirming the current size of each, the proper packer sizes were selected for each hole, and the ROV set forth to prepare each hole to receive its own packer plug. This preparation included inserting a measuring tool into each hole to determine if there was anything blocking the path of the packer as the packers had a minimum insertion length required to make a proper seal. Differential pressure tests were performed to evaluate communication between the holes and learn more about the nature of the leaks. A ROV operated drill was brought in case any of the holes needed to have lodged debris cleaned out, and a ROV operated saw was also brought because the initial inspection showed that one of the holes had a piece of protruding material sticking out that might have required sawing.
Debris Removal and Placement of a Permanent Concrete Bulkhead to Isolate a Leaking Tunnel in a Mine
This project involved a mine in a remote location that flooded when one of the tunnels intercepted an underground water source. The subsequent flooding left much of the mining support equipment in the flooded tunnels and shaft at a depth of approximately 1,300’.
Hibbard Inshore was hired to supply their Sub-Atlantic Mohican vehicle as well as ROV supervisory services to aid in the retrieval of debris and the preparation of the tunnel to receive a permanent concrete bulkhead to allow the mine shaft and tunnels to be pumped dry so that mining could resume on the site. Once the preparation work was complete, Hibbard Inshore also participated in the placement and filling of the bulkhead.
As part of the preparation work, the Mohican was fitted with cutters to help get steel and ducting out of the way as well as to offer support to vehicles provided by another contractor that had become entangled in the debris due to the high volume of hazards, tight quarters, and low visibility.
The failed part of the mine had let water into the rest of the mine and flooded the entire facility. Debris was removed from the opening into the tunnel before the bulkhead was installed. Debris included sand, vent ducts, utilities, front loader and rock bolts. The bulkhead was a large bag 15 feet x 15 feet x 15 feet. This bag was put into place then pumped full of concrete to create a bulkhead. After this was installed, small shafts were drilled from the surface to pump additional concrete into the tunnel behind the bulkhead. Jay Hibbard was onsite for preparation work with ROVs and was onsite for the ROV installation of the bulkhead.
Inspection of Newer Hydroelectric Facilities
In 2010, due to equipment capabilities and previous inspection experience at hydroelectric plants, Hibbard Inshore was hired to inspect two facilities in Bhutan. Hibbard Inshore used two of their specialized ROVs equipped with video cameras and multiple types of sonar to complete the inspections. The purpose of these inspections was to look at the underwater structures of each plant to determine how well they were holding up after they had been commissioned. While one of the plants, Chukha Hydro, had been in operation for some time, the owner also decided to proactively inspect their newer Tala Hydropower Plant. While both facilities had been inspected prior to commissioning, the owner thought it prudent to also inspect them now that they had been operating to determine whether any conditions of concern were present after the introduction of water. This would be the first inspection of these structures since they had been filled.
Figure 1 Hibbard Crew with Long Range Navajo (white) and LBV (Green)
In order to perform the inspections, Hibbard Inshore used two ROVs, a Long Range Sub-Atlantic Navajo with 5 kilometers of tether and a 600 meter depth rated LBV600-6. The combination of these two vehicles allowed Hibbard Inshore to inspect the internal portions of each plant’s underwater structures to look for signs of wear and degradation such as concrete spalling, out of round conditions, cracking, holes, sediment buildup, and debris. During the inspections of the head race tunnels, surge shafts and pressure piping, the Hibbard Inshore ROV saw several small anomalies that were considered “areas to watch” for the future to make sure further degradation wasn’t occurring, and the ROV detected several small holes in the concrete in the bottom of the surge shaft at the newer Tala Facility. After observation with the ROV cameras, it was clear that particulate in the water was being sucked through each of the holes meaning that there were flow paths from inside of the Surge Shaft to underneath the structure. This finding was of great concern to the future stability of the structure. This allowed the dam owner to work with Hibbard Inshore on a plan to permanently plug those holes in 2012 and 2013.
Cable Touchdown Inspection in a High Current Area
This project involved the survey for a cable route as well as a cable touchdown survey for the placement of power and communications cabling from the mainland to a major island through waters with high tidal currents. The cable would stretch over an area of 30 kilometers and would require a powerful ROV to aid the construction team in placing the cables correctly. The power line project survey area crossed the Georgia Strait between Vancouver Island and mainland Canada where currents during operations were in excess of 2 knots. In order to begin each project, the Hibbard Inshore team assesses the survey location for its particular challenges in order to select the optimal vessel, remotely operated vehicle (ROV) and survey equipment spread. Hibbard Inshore has worked for years to develop appropriate methods and equipment to address a wide variety of marine construction and inspection applications, and these projects were no different. The unique challenge for each of these was that while the survey areas were not very deep by ocean standards, the tidal currents were extremely brisk.
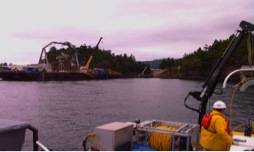
Prior to hiring Hibbard Inshore, the customer had performed a side scan sonar survey to identify a likely route for the cable lay; however, because the side scan head was still quite a distance from the actual bottom, the customer wanted to use an ROV to confirm if several questionable locations would be suitable for the cable placement.
They hired Hibbard Inshore to perform a pre-lay survey including spot checking the planned cable routes through rocky areas and over cliffs to verify the best route had been chosen. Once the pre-lay survey was completed, and the final cable route was confirmed, the customer hired Hibbard Inshore to perform a survey of the cable as it was laid in place. This touchdown survey required an ROV that could maneuver during changing tidal currents to provide uninterrupted cable touchdown location to the lay vessel.
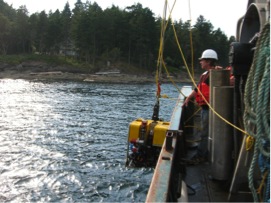
Because of the conditions, the team decided on using the Mohican ROV due to its ability to stay stable in the project environment. The Mohican vehicle was flown in live-boat configuration eliminating the LARS and TMS so a smaller vessel could be used for the project. A full navigation suite was also provided with USBL tracking, GPS, Gyro Compass and IMU. Radio telemetry was provided to send the ROV position and video to the lay vessel.
The Mohican ROV used in these projects has a high thrust to size ratio, and the live-boat configuration reduced the available cross-sectional area of the equipment allowing it to fight the current more efficiently. The live-boat configuration reduced the overall size and weight of the required equipment allowing the use of a smaller crew and small vessel of opportunity. One major advantage was that the vessel did not require a mooring system or a dynamic positioning system to maintain the position of the ROV. Productivity was maximized because time was not required to place and move anchors across the survey area, and the ROV could be deployed very quickly to take maximum advantage of the lower current periods afforded by the change in tides. Additionally, the smaller systems and vessels are comparatively easy to mobilize.
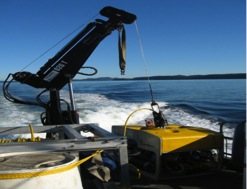
For this project the survey depths ranged up to 200 meters. This sort of ROV and vessel setup can be advantageous for a survey area as small as a single bottom placed sensor or alternatively can be used over a much larger area such as for the Georgia Strait project which required three passes of the entire route for each cable covering a total of approximately 250 kilometers. Due to the selected methods and equipment, the Hibbard Inshore team was able to complete each survey scope within schedule making each project a success despite the difficult currents.
Inverted Siphon Inspection with Crawling and Swimming Vehicles
This project was completed in a 2000 linear foot section of a 96” conveyance line that was buried under a river. The line was dry up until the point where the decline reached river level. Hibbard Inshore brought 2 vehicles to complete this inspection as a crawling vehicle alone would not have been sufficient to navigate the debris in the under-river portion of the line. A launching apparatus was attached to a crawling vehicle which was lowered into the line behind a swimming vehicle.
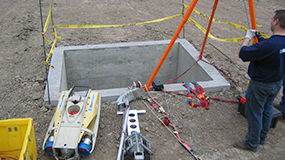
The crawling vehicle was able to push the swimming vehicle several hundred feet to the point where it could launch into the water and complete the inspection by swimming above the debris. The swimming vehicle was able to identify cracks in the concrete pipe using both video and sonar. This methodology allowed the inspection to be done without the aid of confined entry crews being several hundred feet into the line, saving significant cost. The inspection was able to be completed in a single 10 hour shift, and it led to several repair points being identified by the customer.
Tidal Generation and Managing Currents for Underwater Operations
Whether the final product is oil, gas or electricity, sometimes pipelines or cables need to span areas that are not easily conducive to underwater inspection and maintenance operations. These products are extremely important to daily life, and because of this, industry leading companies are constantly improving the equipment and methods necessary to both place these assets and to keep them in good operating condition even in the most challenging areas. Operating around swift ocean currents at depth is one of the tougher challenges presented by the location of many offshore pipelines and cables.
Operations Control Setup
Recently, Hibbard Inshore was contracted to address the seabed assessment, site selection, and cable route survey needs for a tidal generation station in the United States which will consist of two turbines. For each project of this nature, the team assesses each unique survey location for its particular challenges in order to select the optimal vessel, remotely operated vehicle (ROV) and survey equipment spread to fit the project’s needs. The Hibbard Inshore team along with its partners has worked together for years to develop appropriate methods and equipment to address a wide variety of marine construction and inspection applications. This project was no different. The unique challenge here was that while the particular area was not very deep by ocean standards, the tidal currents in the survey area were extremely brisk. The currents had a negative effect on two earlier attempts by others to collect the necessary survey data in the proposed work area. After looking at the situation, the team decided on using a Sub-Atlantic Navajo ROV in a live-boat configuration. This meant that the ROV was run without a tether management system (TMS). The ROV system was coupled with the appropriate navigation and tracking systems for geo-referencing of the data allowing successful completion of the surveys.
Navajo ROV and Support Equipment Loading on to Small Work Vessel
The ROV has a very high thrust to size ratio, and the live-boat configuration reduced the available cross-sectional area of the equipment allowing it to fight the current more efficiently. Further advantages of this method included the use of a small crew and small vessel. The live-boat configuration reduced the overall size and weight of the required equipment allowing the team to also reduce the size of the crew needed to operate the vessel, survey system and ROV. Additionally, the vessel did not require a mooring system or a dynamic positioning system to maintain the position of the ROV allowing for the use of a smaller (45’) vessel. Productivity was maximized because time was not required to place and move anchors across the survey area, and the ROV could be deployed very quickly to take maximum advantage of the lower current periods afforded by the change in tides. Finally, the smaller system and vessel are easy to mobilize and reduce overall associated logistical costs to the customer.
Navajo ROV on Tail of Vessel while Underway
The survey area consisted of three separate passes of the proposed cable lay area of approximately two kilometers per pass along with a survey of the proposed area for the installation of the units which was approximately 100 meters by 150 meters where grid lines were run on ten meter centers. The nominal site depth was approximately 60 meters, and the Hibbard Inshore team was able to complete the full survey scope in three operations days making the project a success despite the difficult currents.