|
Head Gate Seal Inspection - (WMV Video 1.5MB) The head gate seal plate was missing from one of several units on a hydro electric plant. A visual inspection tallied how many bolts were missing, broken, or in place. The ROV also descended into the penstock and into the unit's scroll cage to verify that the missing seal plate was not inside the unit, thus endangering the wicket gates. |
ROV in cage ready to be lowered into water for inspection 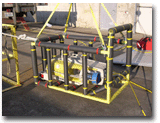
|
|
Internal Outfall Debris Buildup Sonar Model Hibbard Inshore created a sonar model from a dual imaging sonar head system on an ROV from inside an outfall to show how much debris had accumulated and whether or not the diffusers were occluded. The sonar was able to image the end of the outfall despite the lack of cross section at the end that prevented the ROV from passing. We used the model in a flow analysis to determine if the debris buildup was detrimental to the operation of the outfall. |
Sonar record showing diffuser in outfall and debris buildup 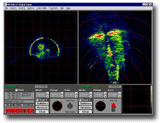 | CAD rendering of pipe for visualization of complex features 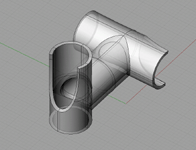 |
Debris buildup at invert of pipe and joint 20 feet ahead of ROV 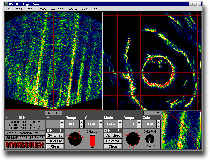 |
|
Internal and External Joint and Support Inspection of Ocean Outfall - (WMV Video 5.6MB) In this project, we used a powerful, 1,500-pound light work class ROV in the strong currents at the deep end of an ocean outfall over the edge of the continental shelf to inspect all supports, external joint conditions, and diffuser conditions. Then divers opened access manways to insert a smaller ROV for an internal inspection of the pipe joints, diffusers, and ball joints. |
Diver inserting pipeline ROV into outfall for internal inspection 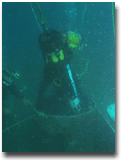 | Diver inserting pipeline ROV into outfall for internal inspection 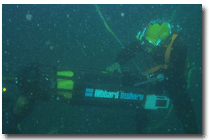 |
Pipeline ROV inside of outfall, not pig stop tab next to ROV 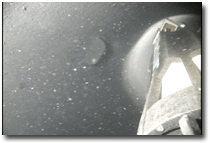 | ROV's Camera view of outfall diffuser from inside outfall 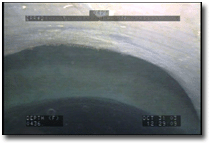 |
|
Internal Tunnel Rock Trap Debris Level and Loss of Cross Section - (WMV Video 2.6MB) Hibbard Inshore conducted an internal inspection of a large power tunnel to determine loss of head condition. First, we determined that the surge shaft contained large cracks. Second, we measured the level of debris in the rock trap by creating a cross section from sonar. Finally, we were able to show that a few large rocks had fallen to the invert from the wall of a rock-cut portion of the tunnel. |
Video record of typical rock in this rock trap 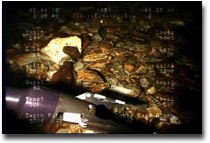 | Large crack in shaft wall at 146-foot depth 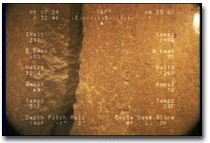 |
View of surge chamber from ROV video camera 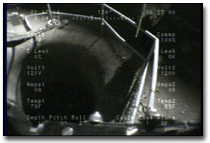 | ROV lowered into surge chamber for shaft inspection 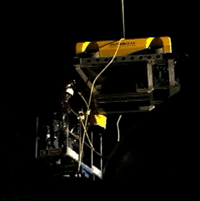 |
Videocapture of three-foot-wide rock (as measured on soar) in tunnel invert 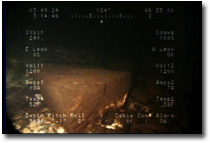 | Sonar of rock trap showing fill level 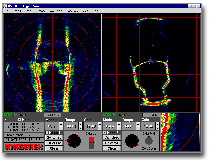 |
|
Wet and Dry Tunnel Inspection by a Crawler In this project, a small crawler visually inspected the interior of dry parts of a pipe and used an ultrasonic thickness (UT) gauge and sonar to image acoustically the flooded pipe sections. |
Sonar of outfall half full and of fisers for diffusers 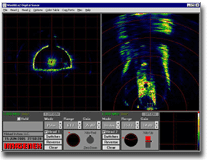 | Crawler entering dry portion of siphon for visual inspection and carrying sonar for wet part of inspection  |
Sonar of round pipe with no significant features 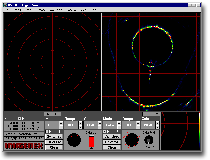 |
|
Internal Laser Alignment of Dry Pipe Using a Crawler - (WMV Video .9MB) Several lower outlets in small retention dams high in the Sierra mountains required assessment. Hibbard Inshore flew the ROV and dive equipment to the area by helicopter. A diver burned open the trash rack and inserted the crawler. The crawler inspected several of the steel lower outlets while flooded visually and with a UT gauge. The crawler also inspected one of the dry outlets visually and measured the alignment using a pipe laser and a target on the crawler. The alignment was performed to determine if the pipe could be lined. |
Crawler exiting lower outlet pipe with laser target 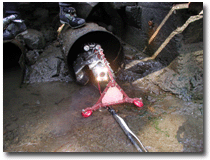 |
|
Sonar Measurement and Modeling Several sonar plots are joined in CAD with blueprint dimensions to produce models of debris buildup or structure deterioration. The sonar references the structure, and absolute measurements or relative measurements can provide a wide range of answers for a structure. |
The ROV placed the sonar to plot the debris buildup against a lower outlet intake structure 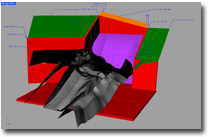 | The structure was approximate in CAD and a diver-held sonar was used to map out failures inside a submerged support colum. The sonar plots showing material loss in the column are in black 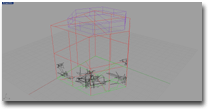 |
A visual representation of the cross section loss of a submerged support. The black lines represent the material lost from inside the column. |